Why do customers need sunlight readable LCD's?
When an LCD is used in a high ambient lighting area, outdoors or even in direct sunlight a normal brightness display becomes almost unreadable. Most people have experienced this phenomenon using their mobile phones, tablets, and notebooks outdoors or when sitting near a window on a sunny day. The display looks hazy, dark, and may even have a halo over the screen. As an individual you have the option to turn the hand-held device to shade it from the bright light to read the information. Could you imagine passing at mid-day by a street-side shop with a display showing their products advertising sales items or specials, but the display can’t be read. The customer would not know what messages the shop is trying to deliver. A missed opportunity to make an impression on a potential customer. All the money spent on the advertisement and equipment but did not capture the attention of the customer because the display was too dark. A sunlight readable LCD displays, also known as a high brightness display are designed to operate in an outdoor setting or in direct sunlight. These products are designed to be very rugged and durable to meet the most the challenging environmental conditions. These are a must have requirement when developing industrial displays used in environments such as oil and gas, marine, military, agriculture where a product must perform for long periods of time.
What is Sunlight Readable display technology?
There are several technical approaches and various enhancement methods to increase screen viewability and reliability in the sunlight. The primary enhancement is to develop a backlight system that increases the brightness of the LCD to overcome a brightly lit environment. There are other technologies that can be added to a high bright backlight such as transflective enhancement (Meaning both Transmissive and Reflective) that will use some of the ambient lighting to make the screen more readable in bright environments. Direct backlighting technology now includes local dimming. This feature concentrates the backlight only in an area where the image needs to be bright further increasing contrast of the LCD display. Other enhancement includes the use of Anti-Reflective and Anti-Glare (AR/AG) cover glass that is optically bonded to the LCD front surface to minimize reflective loss and improve contrast of the display.
High Brightness
Sunlight Readable displays is a core competence of Litemax since the company’s inception. Most displays offered from Litemax include at least a 1,000-nit backlight. Litemax proprietary backlight design, internal heat sinking of the LED junction allows their engineering teams to develop a bright backlight while minimizing over all power and internal heat. This is important for displays used outdoors as brightness is one concern, so is heat built up due to thermal loading caused by the sun. Custom backlights can be developed upon request to even higher brightness of 2,000, 2,500 or even 3,000 nits. The high brightness ensures perfect visual readability under any lighting condition. Below is a table that outlines a brightness that would be suitable based on the environment and application.
- Litemax backlight technology 1000-nits (VHB: Very High Brightness), designed for Outdoor, Sunlight readable applications.
- The normal common brightness of LCD for indoor applications: brightness 250~350nits
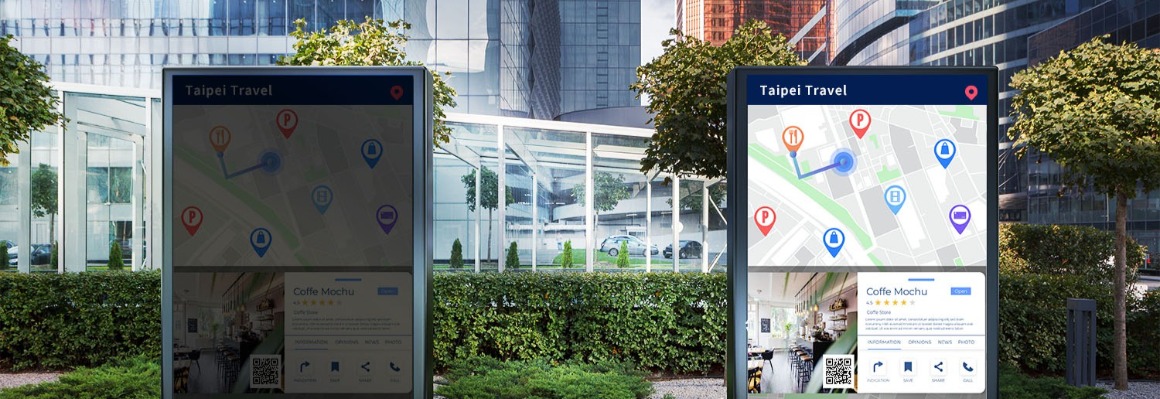
*Table: Lighting conditions and recommended LCD solution
Lighting Condition | Ambient Brightness | Recommended Display Brightness | Application |
Indoor without light | 500 nits | 200 nits | Darkroom |
Indoor with light | 1000 nits | up to 300 nits | PC desktop, building & surveillance monitoring |
Bright shop lighting; Overcast sky | 1000~3000 nits | 300 ~ 500 nits | POS, industrial |
Thin high overcast sky; indirect sunlight | 3000 ~ 7000 nits | 500 ~ 800 nits | Public transport, such as train station, bus stop, airport; semi-outdoor digital signage |
Full sunlight, blue sky | 7000 ~ 10000 nits | 800 ~ 1000 nits | DOOH, KIOSK, Gas station |
Transflective Enhanced LCD
One of the methods for minimizing backlight heat and improving outdoor viewability is to enhance the LCD with a Transflective (transmissive-reflective) layer This layer allows ambient light to be reflected through the LCD display, re-directing the light to make the LCD viewable in a brightly lit situation. This enhancement improvement is one of the state-of-the-art technologies for high-performance color-reduced power consumption for displays used outdoors.
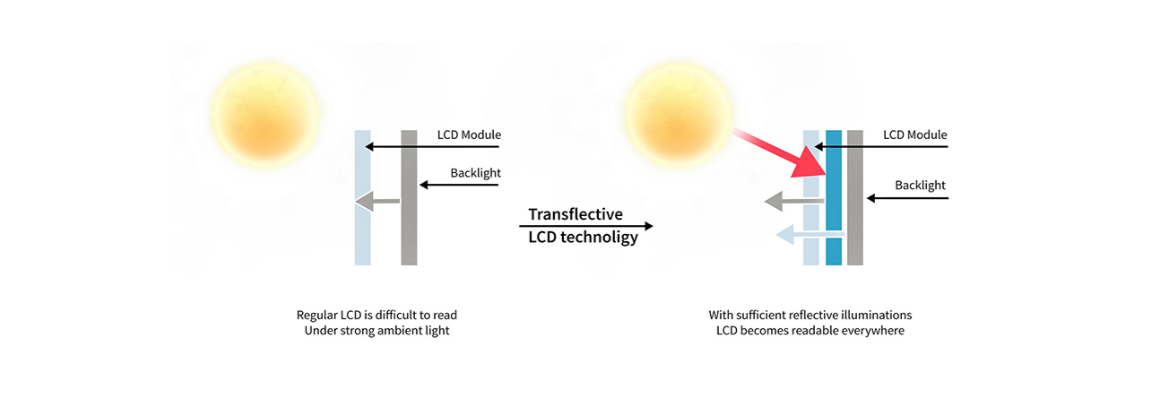
Advanced Optical Bonding (AOT)
AOT (Advanced Optical Bonding) is one of Litemax’s many patents. Optical Bonding is an enhancement that improves readability by minimizing reflective surfaces. This combined with index matching the coatings of the cover element to the adhesive layers further reducing internal reflective surfaces to minimize reflective loss creates the brightest, clearest rich images available in an outdoor display product. AOT is the use of an optical-grade adhesive to laminate anti-reflection glass, touch screens, heaters, and EMI shields to the top surface of a display. This method eliminates the air gap between the cover glass and the display enhancing readability in sunlight. The other advantage of optical bonding is to fill in the air gap where moisture can accumulate in high humidity outdoor environments and the display’s ability to resist impact damage improves significantly. As the pioneer in sunlight readable displays, Litemax strives to develop new leading-edge products and processes for use in the most demanding market segments. These enhancements help overcome the challenges our customers face when deploying a display in a rugged outdoor environment.
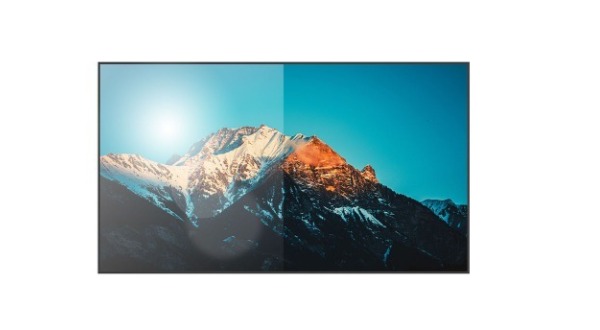
Improve readability
Increased the contrast ratio up to 4 times by minimizing reflective loss
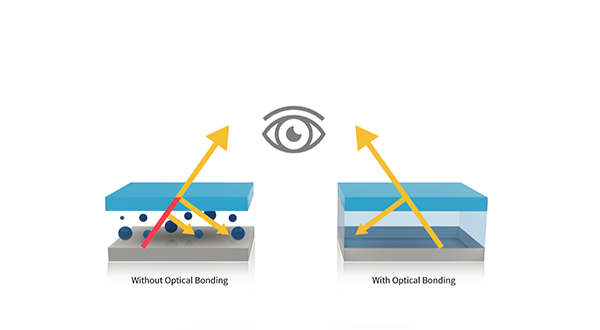
Reduce reflection
Optical-grade adhesive that is index matched used to laminate a customized cover glass element to the front surface of the LCD.
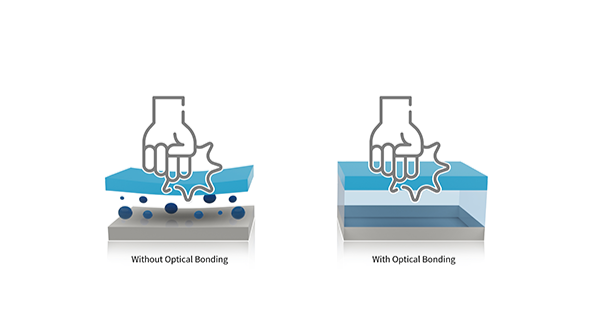
Enhance ruggedness
The elimination of an air gap between the cover glass and the display preventing moisture from entering that could cause fogging on the display's surface.
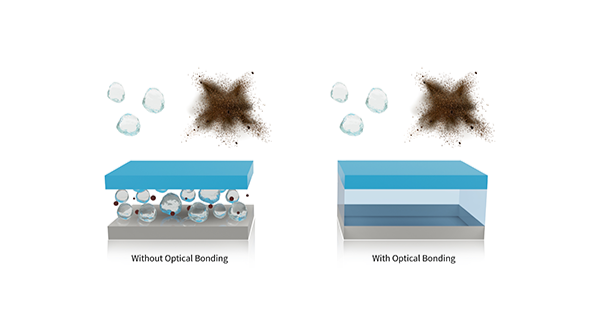
Dust & moisture protection
Optical-grade adhesive that is index matched used to laminate a customized cover glass element to the front surface of the LCD.
UV protective film & IR heat rejected
Most of the energy that reaches the Earth’s surface comes from the Sun. Solar radiation is in the visible light wavelengths that we can see. The Sun also emits infrared, ultraviolet, and other wavelengths of energy that is invisible. Of the solar energy that reaches the earth, UV wavelengths have the greatest energy. The remaining solar radiation is the longest wavelength, infrared. Most objects radiate infrared energy, which we feel as heat. This heat can be absorbed by a display when it is in direct sun light. This absorption of the external heat is known as solar loading or thermal loading. To combat solar loading Litemax has developed unique materials and process to add as enhancements to minimize the heat that can build up in the LCD from being exposed to direct sun light. One of the technologies is Anti UV/IR Coatings. Using these coating technologies improves the total solar energy rejection from a Litemax display. This can be up to 53% rejection of these invisible solar allowing the LCD to perform in the most demanding locations.
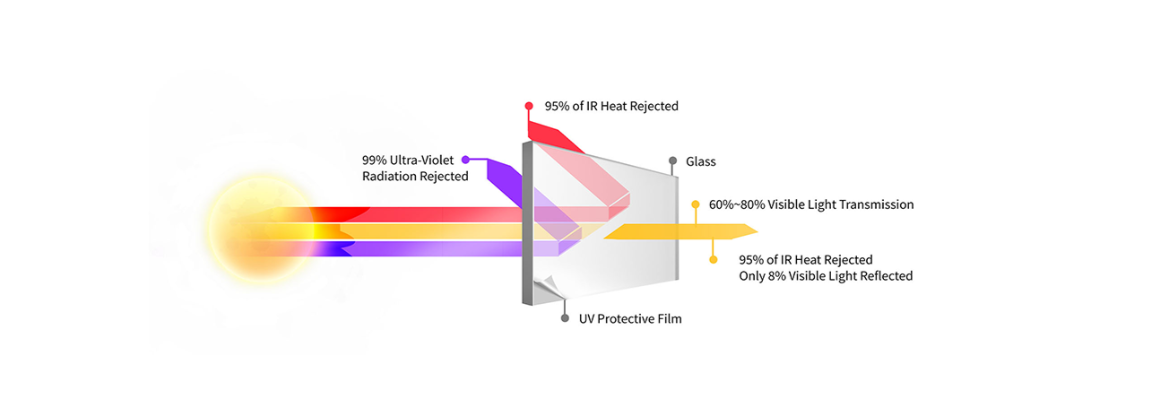
Local Dimming
Local dimming technology has been widely popular in mainstream television for years. Litemax has brought the same technology to our large sized industrial-grade outdoor displays. Local dimming dims the LED backlight to optimize the heat and save energy. Litemax also achieves High Dynamic Range (HDR) through local dimming technology to enable the industry’s greatest color contrast in the industry.
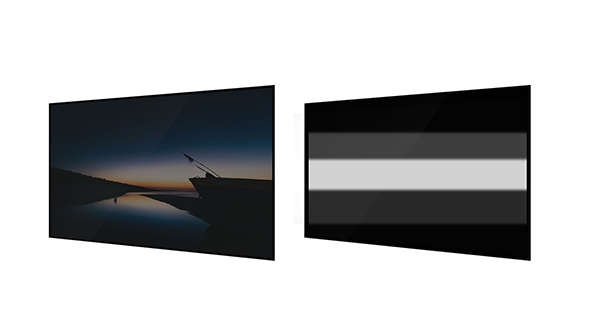
Conventional
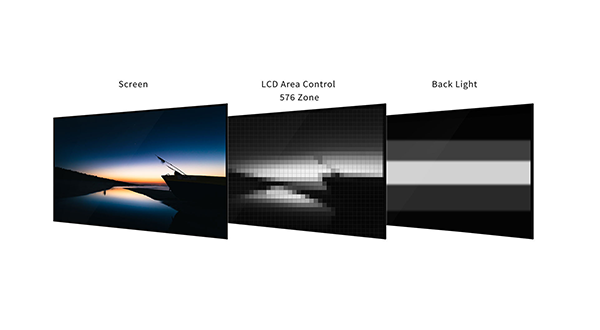
Local Dimming
MTBF
The LED-backlit displays boast high-end features, such as lower electromagnetic noise, wide dimming range, and lower power consumption. These backlight systems are developed to output high brightness but also to increase the lifetime of the LED. This design approach and through testing means Litemax backlight systems are one of the most robust designs available in the market. These high bright backlight systems include a Mean Time Between Failures (MTBF) of 100,000 hours. This exceeds typical longevity requirements for industrial-grade applications that require continuous operation and minimal maintenance.
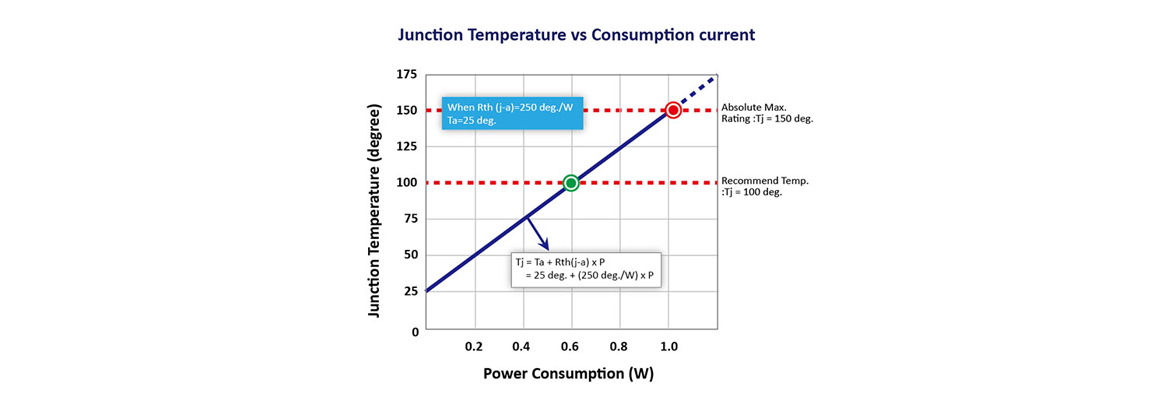